Eyelet welding
Frequently asked questions about eyelet welding
The invention of the metal eyelet in 1828 was intended to reinforce women’s corsets, which were rapidly deteriorating, despite the mending of embroidered eyelets (through-holes), due to the pressure exerted by the laces. In fact, the lacing system used to bring the ends of the two textile pieces together exerted such tension on the entry and exit holes that it caused the fabric to tear. The material used at the time was steel, and the diameter of the eyelet was small, as it was only intended to allow the passage of a thin cord so that it would not be perceptible under the upper garment.
During the twentieth century, the eyelet left the corsetry field to become a key element of fastening or suspension systems in many sectors of activity. In this context, the manufacture of metal eyelets diversified considerably, with a wide variety of internal and external diameters, as well as the invention of the threaded eyelet, the tube eyelet, the eyelet bolt with nut…
At the same time, new materials became increasingly important in eyelet production, with the use of rubber and rigid plastics. In the field of installation and fastening methods, the eyelet welding technique in particular was developed.
What are the different eyelet techniques?
The fastening techniques depend both on the nature (metal, plastic…) of the rings to be fitted and on the materials to which they are to be inserted . The methods most commonly used in different industrial sectors are :
- Manual crimping with dedicated pliers or a specialized press for thin-walled metal or malleable metal (brass, copper, aluminum, etc.) eyelets.
- The welding of plastic eyelets (PP, PVC, PU…) to sheets of similar materials using manual electrode welders, high-frequency welding presses or ultrasound.
- The clipping of plastic rings with manual grippers, which can perform both punching and insertion operations.
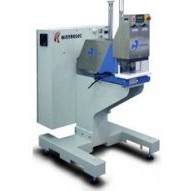
What materials can be used to make eyelets?
Since the invention of the carnation in the 19th century, its production has evolved considerably, both in terms of quantity, given the growing number of uses, and in terms of quality, with the mechanization and automation of its manufacture.
The production of fastening rings is now based on the use of a large number of raw materials:
In the family of metals, stainless steel, aluminum, brass and aluminum-zinc have been added to steel.
- The plastics family includes Polypropylene (PP) Polyethylene (PE), Polyurethane (PU), Polyvinyl chloride (PVC), Acrylonitrile Butadiene Styrene (ABS) and Ethylene Vinyl Acetate (EVA).
- Rubber is increasingly used in the automotive sector, with its own specifications.
What's the advantage of a plastic eyelet over its metal counterpart?
Plastic rings can be used to create more attractive fasteners or suspensions than their metal equivalents for certain products and applications:
- These plastic eyelets combine great strength with a certain flexibility.
- The absence of rust avoids problems of soiling or streaking caused by exposure to the elements or use in damp environments.
- Welded eyelets ( PVC, PU…) are all the more resistant as the assembly technology fuses the material they are made of with the material to which they are to be attached.
- The plastic rings can be positioned on the back of the banner they’re attached to, making them invisible to the naked eye once attached.
Produced in a variety of colors, the plastic eyelet has also acquired an aesthetic dimension with its use in the fashion sector to create designs and patterns on garments or pieces of luggage.
How do I weld a plastic eyelet?
Specializing in the design and manufacture of parts made from sheets of PVC, PU or reinforced materials, Carmo has developed at both the production of weld eyelets and equipment for punching and fastening operations.
The Danish company has developed several methods of installing the rings on the surfaces to be fitted, transforming them into welded eyelets. A thin joint is created around the hole in the center of the eyelet, by fusing the materials making up the two elements to be assembled. The following ring assembly techniques have been developed:
- Adhesive bonding with polyvinyl chloride particles.
- High-frequency welding with electrodes for punching and assembly.
- Clipping for the very specific category of clip eyelets.
In the field of high-frequency welding, which is the method most widely used by Carmo, the company has developed several families of equipment for craft and industrial production:
- Lightweight welders for manual use, with quick and easy electrode changes to suit the diameters of the rings to be joined.
- Continuous punching and welding machines using high frequency to ensure single-sided fusion of plastic eyelets.
- high-frequency presses for fast welding of both ring faces with an automatic supply system.
- Inserts with cutting and welding electrodes for installation on a bar welder or HF welding press are already in production.
Which product ranges feature eyelet fasteners?
These suspension or fastening systems are used in a wide range of sectors and product families . For the sake of convenience, we have grouped them according to a product typology we have developed:
- Fittings (sails, etc.) for sailboats and surfboards.
- Protective and safety tarpaulins for transport vehicles or buildings under construction.
- Advertising banners: banners, kakemonos, signs, banners, flags, beachflag…
- Tents for camping and events (tents, marabouts, barnums, marquees…).
- Home textiles (shower curtains, sheers, blinds and curtains, pergolas…).
- Accessories and parts for vehicles and transport: cable grommets, sheath grommets, wire grommets…
- Clothing (pants, dresses, tunics, jackets, sweaters, coats, corsets, swimwear…).
- Footwear (boots, brodequins, sneakers and other lace-up shoes, safety shoes, etc.).
- Fashion accessories (backpacks, handbags, clutches, belts, harnesses, etc.).
What materials can be used to make eyelets?
Since the invention of the carnation in the 19th century, its production has evolved considerably, both in terms of quantity, given the growing number of uses, and in terms of quality, with the mechanization and automation of its manufacture.
The production of fastening rings is now based on the use of a large number of raw materials:
- In the metals family, stainless steel, aluminium, brass and aluminium-zinc have been added to steel.
- The family of plastics includes Polypropylene (PP), Polyethylene (PE), Polyurethane (PU), Polyvinyl Chloride (PVC), Acrylonitrile Butadiene Styrene (ABS) and Ethylene Vinyl Acetate (EVA),
- Rubber is increasingly used in the automotive sector, with its own specifications.
What's the advantage of a plastic eyelet over its metal counterpart?
Plastic rings can be used to create fasteners or suspensions that are more attractive than their metal equivalents for certain products and for certain fields of activity :
- High strength is combined with a certain flexibility thanks to the plastic nature of these eyelets,
- The absence of rust avoids problems of soiling or traces linked to exposure to the elements or to use in a damp environment,
- The strength of welded eyelets is enhanced by the fact that the assembly technology used fuses the material of which they are made with the material to which they are to be attached,
- The plastic rings can be positioned on the back of the banner on which they are mounted, making them invisible to the naked eye once they have been attached.
Produced in different colors, plastic eyelets have also acquired an aesthetic dimension with their use in the fashion sector to create designs and patterns on garments or pieces of luggage.
How do I weld a plastic eyelet?
Specializing in the design and manufacture of parts made from sheets of PVC, PU or reinforced materials, Carmo has developed at both the production of weld eyelets and equipment for punching and fastening operations.
The Danish company has developed several methods of installing the rings on the surfaces to be fitted, transforming them into welded eyelets. A thin joint is created around the hole in the center of the eyelet, by fusing the materials making up the two elements to be assembled. The following ring assembly techniques have been developed:
- Adhesive bonding with polyvinyl chloride particles
- High-frequency welding with electrodes for punching and assembly,
- Clipping for the very specific category of clip eyelets.
In the field of high-frequency welding, which is the method most widely used by Carmo, the company has developed several families of equipment for craft and industrial production:
- Lightweight welders for manual use, with quick and easy electrode changes to suit the diameters of the rings to be joined,
- Continuous punching and welding machines using high frequency to ensure single-sided fusion of plastic eyelets,
- high-frequency presses for rapid welding of both ring faces with an automatic supply system,
- Inserts with cutting and welding electrodes for installation on a bar welder or HF welding press are already in production.