Rotary tables
Frequently asked questions about rotary tables
What is a rotary table?
Used above all in industry, they are used to assist mass production of parts of all sizes, or to assemble sub-assemblies, thanks to their axis(s) of rotation. In fact, they can be integrated or deployed on numerous numerically-controlled machines: machining centers, lathes, milling machines, grinding machines, pillar drills, polishing machines, laser markers, welding presses, metrology equipment….
Schematically, a rotary table can be defined as a device comprising at least a rotary table and, more often than not, a high-precision motor. The following configurations are possible:
- a manual, electric or pneumatic tray guide system,
- motorization by a torque motor, a motor with reduction or a stepper motor,
- independent speed reduction thanks to a dedicated gearbox,
- static braking to immobilize workpieces or parts to be assembled,
- an automated control system for maximum repeatability.
Other important features of the tables are the diameter of the tabletop, and the precision and repeatability of the rotation in order to meet the exact handling requirements of the parts to be produced or modified.
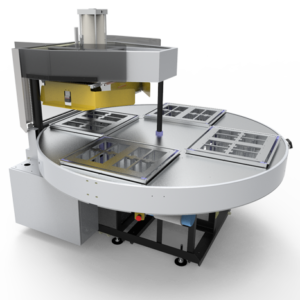
What's the difference between rotary and transfer tables?
Although they play very different roles, as we shall see later, these two types of equipment are designed to enable complete automation of the production tool, in the manufacturing or assembly fields. In fact, both families of ” industrial tables ” are production-assistance devices that can be integrated in a variety of ways:
- installation or assembly of ready-to-use tables on existing machine tools,
- design and development of specific tables by machine tool manufacturers or their specialist suppliers.
The essential differences lie in the role played by each of these two devices and in the level of technology used by their manufacturers:
- While rotary tables perform the precise positioning of parts to be machined or modified at a single angle or on several axes with a machine tool, the transfer table ensures the regular movement on a vertical plane of products for assembly operations.
- While rotary tables are equipped with motorization and a high-precision guidance system with computer control , transfer tables or platens can be operated manually or with conventional electric motors.
What operating modes are available for rotary tables?
Depending on requirements and technological constraints, the choice of a rotary table must take into account specific features such as indexing mode (actuation), configuration and type of drive.
There are three indexing modes, each with very different characteristics :
- Manual actuation can be used on conventional machine tools for small production runs or slow production cycles.
- Pneumatic actuation is used for small pallet or table-top tables to be installed on machine-tools with limited space. The downside is limited rotation range and therefore limited angle adjustment.
- Electric actuation is used on most rotary tables, whether equipped with a table top or a single pallet. This type of indexing enables tables to be built with a wide adjustment angle and high torque.
The configuration of the table top is a decisive factor in meeting the needs of production. If it has a single axis, it will rotate or on a horizontal or vertical plane. Some tables are said to be tiltable, as they are equipped with a plate or pallet that can rotate on two different axes.
The drive modes of the rotary table have a very strong impact on the potential performance of rotary tables:
- The drive via a bearing with precision bearings and a worm gear reducer provides both a high level of rotational precision in both directions and high resistance to radial shocks associated with material processing or assembly operations.
- The direct drive of the table by the motor generates very high rotation speeds, enabling very high work quality, particularly for machining and surfacing. More cumbersome than worm tables for the same work surface, this equipment requires less maintenance, but needs a specific interface to control its motorization.
What kind of controls are needed for rotary tables?
Only a precise definition of rotary table control requirements, prior to deployment, will enable to define the automated control system to be deployed. This is a function of the nature of the operations to be carried out by the machine tool, the length of production cycles and the frequency of rate changes.
There are three types of rotary table control systems:
- The table has its own control system which operates independently from that of the CNC machine. The parameterization options are simple but limited, and cannot be used with machine tools performing complex operations.
- The table is equipped with a servomotor connected to the machine tool’s control system to ensure its control. A servocontrol unit is used to record the various rotation programs according to the production sequences of the CNC machine.
- The table has neither an independent control system nor a servomotor to ensure its operation or programming. Instead, it is controlled by the machine tool’s control system, which controls the entire installation.